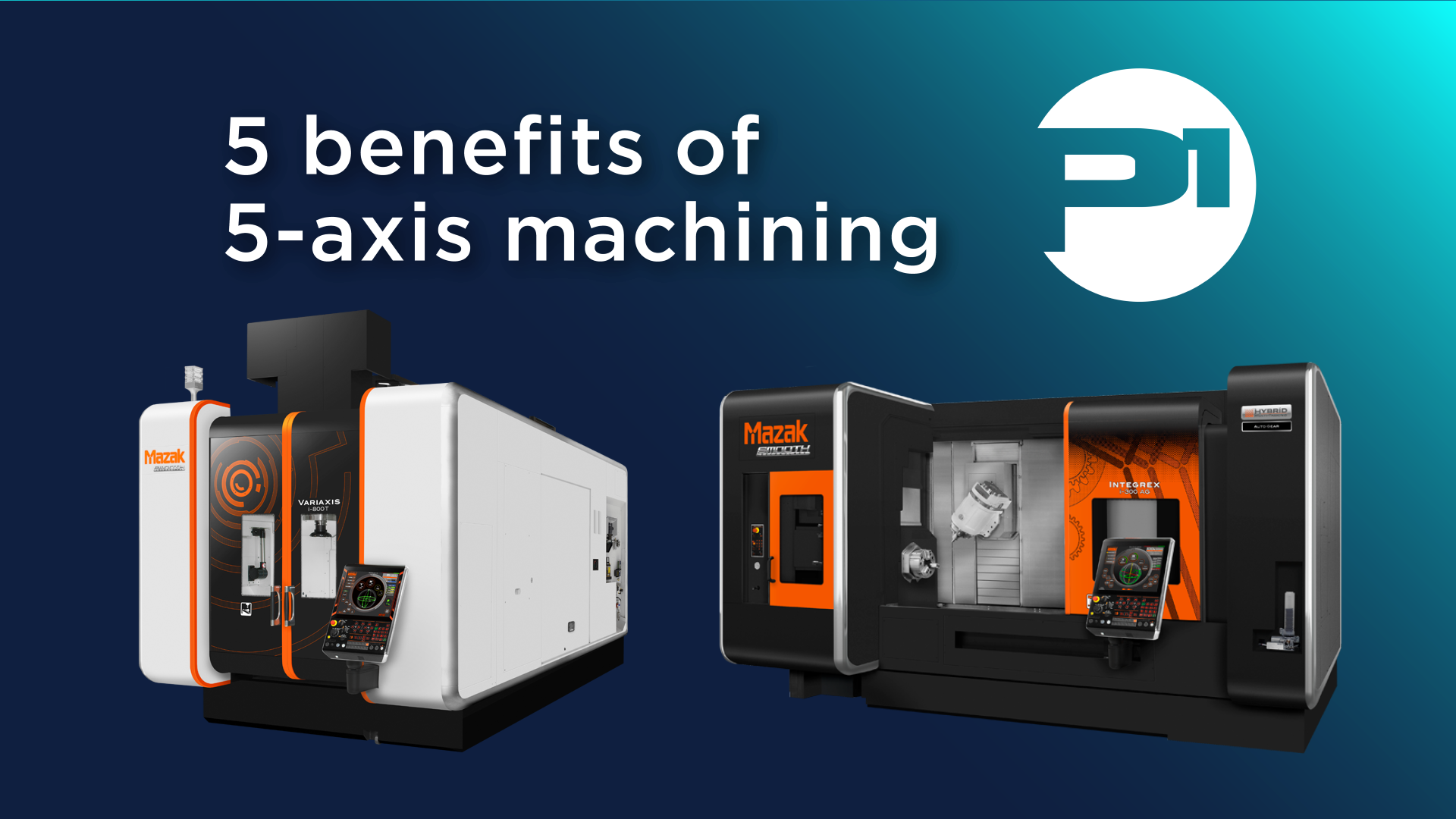
The machines a manufacturing company utilizes, alongside the calibre of it’s people, makes all the difference in being able to fulfill customer requirements for custom parts. And 5-axis machines are particularly necessary when it comes to delivering highly complex parts on time and on budget.
5-axis machining refers to the ability of a machine tool to move a workpiece in five different axes simultaneously, providing several benefits compared to traditional 3-axis machining:
- Improved precision and accuracy: 5-axis machining allows for more precise machining of complex shapes and contours, as it enables the cutting tool to reach all areas of the workpiece.
- Increased productivity: 5-axis machining can reduce the need for multiple setup operations, as it can machine the workpiece from various angles in a single setup. This can lead to a significant increase in productivity.
- Increased material utilization: 5-axis machining can enable more efficient use of raw materials, as it allows for machining from multiple angles, which can result in less waste.
- Enhanced flexibility: 5-axis machining can be used to machine a wide range of parts and materials, making it a versatile option for many different manufacturing applications.
- Improved surface finish: 5-axis machining can produce a higher quality surface finish compared to 3-axis machining, as it enables the cutting tool to follow the contours of the workpiece more closely.
We’re pleased to have two 5-axis machines at P1, enabling us to produce the highly complex, customized parts our customers need. Both the Variax i-800T and Integrex i-300 (plus a third machine arriving soon) are utilized to full capacity by our highly trained machinists to make complex parts for the Oil & Gas, Energy and Defence indistries.
Learn more about our capabilities and feel free to request a quote for the custom parts you require.